Posted 20 May 2024 14:39 | 1,579 views
Basically, to control the environment to decrease the probability of ESD damage in "Class Zero" situations involves increasing ESD protective redundancies and periodic verifications to those ESD Control technical elements.
ESD CONTROL PROGRAM CONSIDERATIONS WHEN DEALING WITH CLASS ZERO ITEMS
ANSI/ESD S20.20 Foreword states:
- "This standard covers ... electrical or electronic parts, assemblies and equipment susceptible to damage by electrostatic discharges greater than or equal to 100 volts Human Body Model (HBM)."
- "When handling devices susceptible to less than 100 volts HBM, more stringent ESD Control Program Technical Requirements may be required, including adjustment of program Technical Element Recommended Ranges."
HMB Classification Class 0 is per ANSI/ESD STM 5.1 Human Body Model (HBM) Table 1 Class 0 has ESD Withstand Voltage Range < 250 Volts
Basically, to control the environment to decrease the probability of ESD damage in "Class Zero" situations involves increasing ESD protective redundancies and periodic verifications to those ESD Control technical elements.
Improved Grounding
- Worksurfaces: Dissipative (CDM) i.e. change < 10^9 to a requirement of 10^6 to 10^8 ohms
- Bonded grounds - Carts, shelves, mobile equipment
- Conductors: Minimizing isolated conductors like devices on PC Boards (CDM)
Personnel: Decrease Wrist Strap and ESD Footwear upper limit permitted (The ESD Association has test data showing charge on a person is less as the path-to-ground resistance is less). The use of continuous monitors, ESD smocks, use / increased use of ESD flooring, sole or full coverage foot grounders (HBM & CDM)
Minimize Charge Generation
The best form of control is to minimize charge generation. Grounding and ionization eliminate charges once generated. Shielding protects from generated charges.
- Personnel - Low Charging floor finish
- Surfaces - Use of low charging topical antistat treatments
image: i0.wp.com/scs-static-control-solutions.blog
Insulators
- Eliminate as best as possible all non-process necessary insulators
- Topically treat where ever possible insulators that cannot be removed
- Replace regular production supplies and fixtures with dissipative, low-charging versions
- Consider use of ESD Chairs or treat surfaces to reduce charge generation
- Shield charges on clothing by using ESD Smocks
Ionization
- Can be critical to reduce induction charging caused by process necessary insulators (CDM)
- Can be critical is eliminating charges on isolated conductors like devices on PCBís (CDM)
- Offset voltage (balance) and discharge times are critical considerations depending on the actual application (CDM).
- Ionization can reduce ElectroStatic Attraction (ESA) and charged particles clinging and contaminating products.
This can mean ionizers with better offset voltage (balance) feedback controls, alarm capabilities, increased (faster) discharge (neutralization) capabilities
Dissipative items (>1.0 X 10^4 and < 1.0 X 10^11 ohms)
- Consideration of optimal range for surfaces (> 1.0 X 10^6 and < 1.0 X 10^9 ohms RTG)
- Gloves / Finger cots: Less conductive than human skin (HBM)
- Surfaces: Minimize conductive surfaces (CDM)
Defining and controlling areas that are considered "ESD Protective"
- Label or otherwise identify ESDS "Class 0" devices as requiring handling only at "Class 0" ESD protective workstations
- Minimize insulators (>1.0 X 10^11 ohms)
- Shielding packaging/handling materials for ESDS items when outside of ESD Protective area
- ESDS item in intimate contact with dissipative & low charging materials (> 1.0 X 10^4 and < 1.0 X 10^11 ohms). Low charging is a material characteristic that is independent of resistance
- ESD worksurface max resistance of <10^9 ohms RTG may be reduced to <10^8 ohms RTG
Increase Training
- Supervisor & line worker ESD Awareness Training
- Testing to verify the effectiveness of the ESD Training program
- Training on proper compliance verification procedures
- Training on the proper use of equipment used for verification
Enhanced Compliance Verification Plan with possible greater frequency of internal audits
- Use of Computer data collection system for wrist straps and foot grounders testing
- Increase testing frequency of personnel grounding devices from once per day to every time the operator enters the class zero area
- Use of continuous monitors where operators are grounded via wrist straps. Consider computer-based monitor data collection system. This should include continuous monitoring of the mat ground.
- Use of Ground Continuous Monitors - At a large facility, the most frequent reoccurring violation was ESD mat ground cord either becoming disconnected from the mat or grounding point. While these will only test the fact that the mat is grounded, it is still imperative that the RTG of the mat is regularly tested. The use of improper mat cleaners can raise mat surface resistance above the upper recommended level of <10^9 ohms RTG
- Test ionizers more frequently, consider self-monitoring ionizers, consider computer-based data collection
- Increased use of static field meter and nano coulomb testing to verify that automated processes (like auto insertion, tape and reel, etc) are not generating charges above acceptable limits.
Contact us
Tel.033-641800 089-2534241
email: sales@mostori.com

source: descoindustries.com
#mostorigroup #desco #emit #smartlog pro #partnerthailand
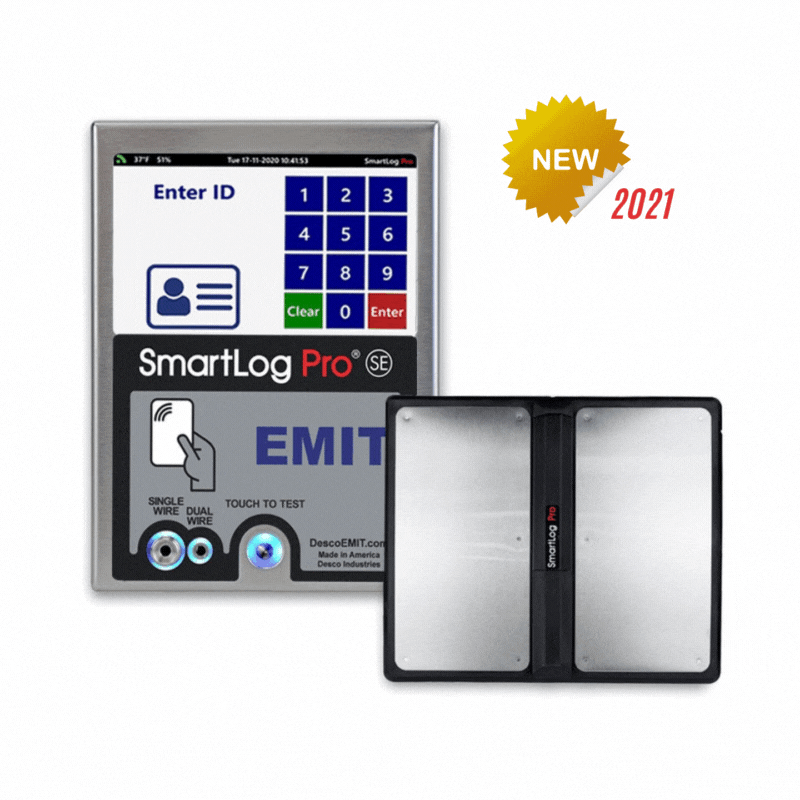
50170
|
.gif)
50172
|
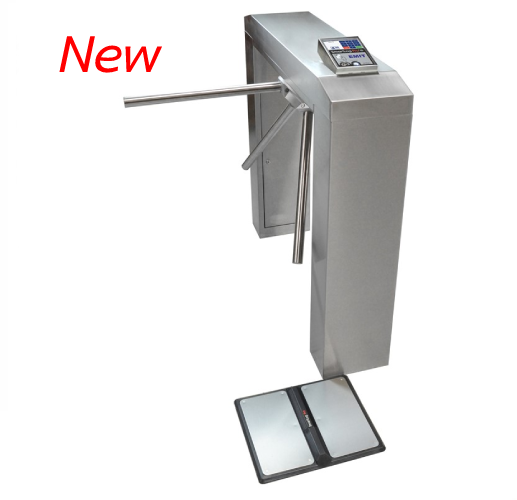
50173
|
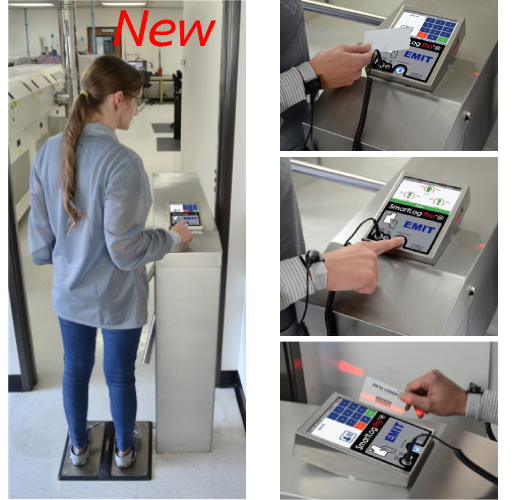
50174
|
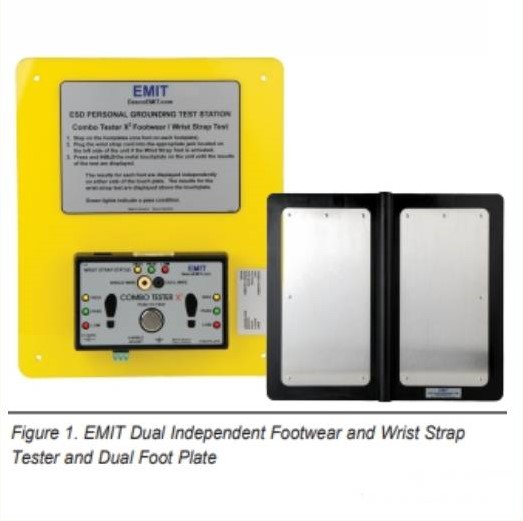
50413
|
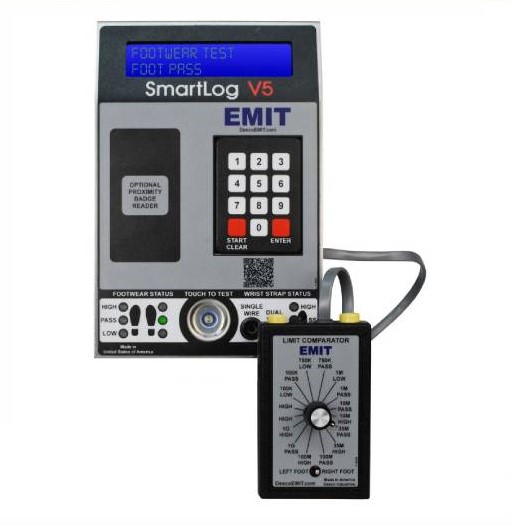
50424
|
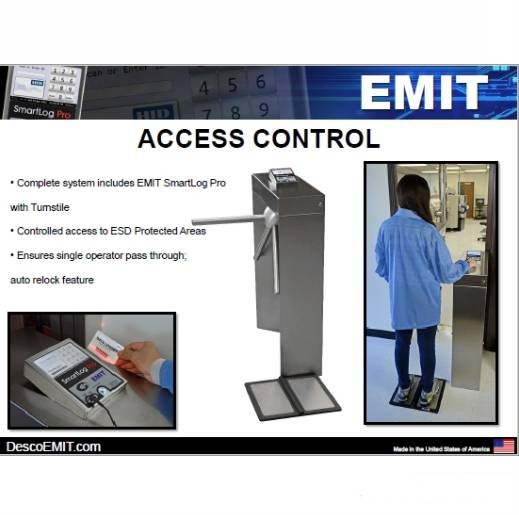
50772
|
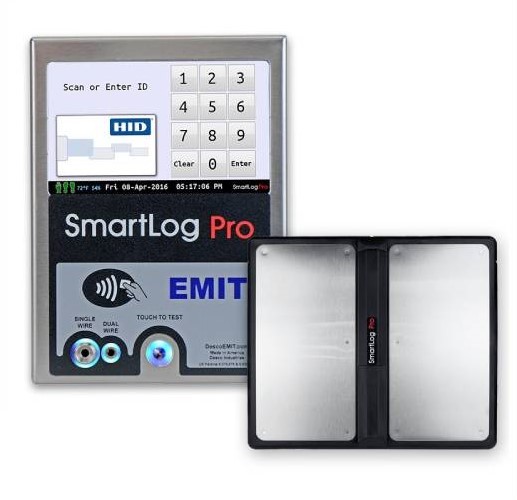
50780
|
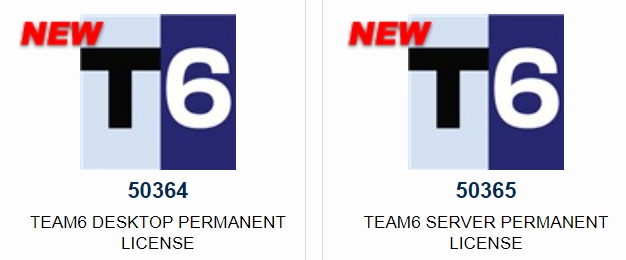
TEAM 6
|